/
Rotax-Motoren: So entstehen die Antriebe für die Allgemeine Luftfahrt
Rund 5000 Flugmotoren fertigt BRP-Rotax jährlich im österreichischen Gunskirchen. Beim Interviewtermin im Werk haben wir einen Blick in die Produktion geworfen und viele Fragen und Mythen rund um die weit verbreiteten Boxermotoren geklärt.
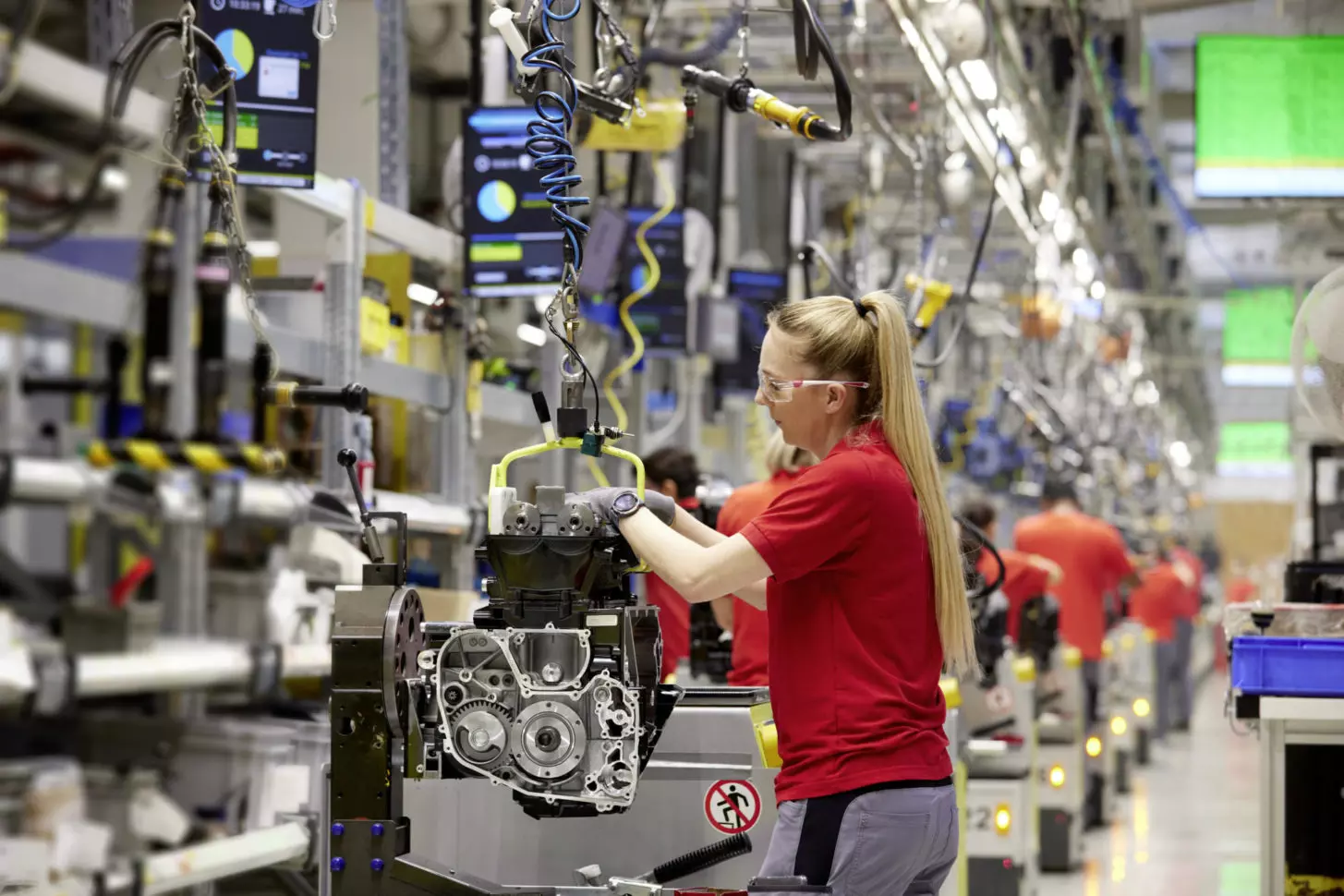
Den Namen Rotax verbinden die meisten Piloten mit Ultraleichtflugzeugen und Echo-Klasse-Zweisitzern. Dabei startete der Betrieb 1906 in Dresden mit der Produktion von Freilaufnaben für Fahrräder. Die heißt auf Lateinisch »Rotanda Axis« – so entstand der Markenname Rotax. 1947 bezogen die Rotax-Werke AG ihren heutigen Standort im österreichischen Gunskirchen nahe Linz. Mitte der siebziger Jahre begann der Einstieg in den Luftfahrtmarkt.
Die Zweitakter vom Typ 642, 503 und 582 werden schnell zur Standardmotorisierung für Trikes und ULs. Erst 2022 stellt Rotax die Produktion des letzten Zweitakt-Triebwerks für die Luftfahrt ein. Ende der achtziger Jahre kommt der Rotax 912 auf den Markt. Der Viertakt Boxermotor mit vier Zylindern und Doppelvergaser legt die Basis für das aktuelle Flugmotorenprogramm. Seit 2003 gehört BRP-Rotax zum kanadischen Unternehmen Bombardier Recreational Products (BRP). Doch genug der Historie. Springen wir wieder ins Hier und Jetzt.
Zu Besuch bei BRP-Rotax nahe Linz
Wer das Werk von innen besichtigen möchte, kommt an einer Online-Sicherheitsschulung nicht vorbei. Dabei bleiben dem Redakteur drei Fakten im Gedächtnis:
1. Ohne Sicherheitsschuhe und Schutzbrille ist die Produktion tabu.
2. Kein Schritt übers Werksgelände ohne Begleitperson.
3. Filmen und Fotografieren sind verboten.
Ganz im Gegensatz zum etwas »garstigen« Sicherheitshinweis ist dann der herzliche Empfang in der Eingangshalle von BRP-Rotax. Hier warten Marc Becker (Manager Aircraft Business), Andreas Bangerl (Manager After Sales Service) und Bettina Hintersteininger (Group Leader Communications).
Im Foyer finden sich die historische Freilaufnabe und zahlreiche Fahrzeuge vom Schneemobil übers ATV bis zum Elektromotorrad. Denn nur rund ein Prozent aller gefertigten Rotax-Motoren geht in die Luftfahrt. Wir betreten in Schutzausrüstung die Werkshallen und laufen in Richtung der Flugmotorenfertigung. Neben dem modernen Maschinenpark fällt der hohe Anteil an manuellen Arbeiten auf. Die Montage der Motoren vom Block über die Zylinder bis zum Verlegen von Leitungen und Kabeln ist Handarbeit. Bis zu 45 Minuten verweilt ein Motor an einer einzelnen Station. Da die Mitarbeitenden rotieren, können viele Arbeiter einen kompletten Motor zusammenbauen.
Was wird alles im BRP-Rotax-Werk hergestellt?
Die zahlreichen manuellen Montagestationen haben einen Grund: Die Produktionsrate ist im Vergleich zur Autoindustrie gering. Dazu kommt eine große Variation vom einfachen Vergasermotor bis zum Turbotriebwerk mit Einspritzung. Womit wir bei einem weiteren spannenden Detail wären: der Fertigungstiefe. Zwar kauft BRP-Rotax Teile wie Kolben oder Rohlinge für die Kurbelwellen zu, bearbeitet sie jedoch aufwendig im Haus. Auch ein Großteil der Turbolader wird im Werk selbst hergestellt.
Alle Flugmotoren durchlaufen in jedem Produktionsschritt engmaschige Kontrollen. So wird dokumentiert, welche Einzelteile zu einem Triebwerk verbaut wurden und welche Personen an der Fertigung beteiligt sind. Auch die Drehmomente von Schraubverbindungen werden automatisch erfasst. Alle Motoren absolvieren vor der Auslieferung auf dem Teststand einen Probelauf. Die Dokumentation endet mit einer Fotoserie vom Motor in der Transportverpackung. Zum Schluss wird ein digitaler Zwilling jedes ausgelieferten Flugmotors erstellt. Hier wird es Zeit nachzufragen. Bei Fly ins habe ich immer wieder Spekulationen über Qualitätsunterschiede zwischen zertifizierten Motoren für die Echo-Klasse und nicht-zertifizierten Triebwerken für ULs und Experimentals gehört.
Andreas Bangerl kennt die Diskussionen am Lagerfeuer. »Es gibt keine Unterschiede in der Fertigung, auch die verwendeten Teile sind immer die gleichen. Der Kunde legt mit seiner Bestellung fest, ob ein Antrieb als zertifizierte oder nicht-zertifizierte Version gebaut wird. Die Preisunterschiede resultieren aus dem Aufwand für die Dokumentation, das unterschiedliche Haftungsrisiko des Herstellers und leicht abweichende Verfahren beim Motorentest auf dem Prüfstand.« Es gibt also definitiv keine nachträgliche Sortierung in zertifizierte und nicht-zertifizierte Varianten. Seit dem Start der 912er-Serie haben über 82.000 Viertaktmotoren das Werk in Gunskirchen verlassen, wo alle Flugmotoren von BRP-Rotax entstehen.
Rotax 912 UL: Beim Einstiegsmotor mit 1211 cm3 Hubraum übernehmen zwei Gleichdruckvergaser die Gemischaufbereitung. Das Triebwerk ist luft- und wassergekühlt. Die Startleistung beträgt 80 PS bei maximal 5800 Umdrehungen. Wie bei allen Rotax-Triebwerken wird der Propeller über ein Untersetzungsgetriebe angetrieben. Die TBO liegt bei 2000 Stunden. Rotax 912 ULS: Die nächste Leistungsstufe bringt 100 PS Startleistung bei ebenfalls maximal 5800 Umdrehungen. Die höhere Leistung verdankt der Vergasermotor dem auf 1352 cm3 erhöhtem Hubraum. Äußerlich ist die stärkere Version an den grünen Zylinderkopfdeckeln leicht zu erkennen. Auch bei diesem Motor liegt die TBO bei 2000 Stunden. Rotax 914 UL: Das erste Turbotriebwerk von Rotax liefert 115 PS Startleistung bei 5800 Umdrehungen. Es hat zwei Gleichdruckvergaser. Der 914 UL ist aus dem 80-PS-Motor durch Integration des Turboladers entstanden. Der Motor verfügt über eine Wastegate-Steuerung gegen Überdruck, die Zylinderkopfdeckel sind rot. Die TBO beträgt 2000 Stunden. Rotax 912 iS Sport: Hier erfolgt die Gemischaufbereitung durch eine elektronisch gesteuerte Einspritzanlage, was sich positiv auf den Verbrauch auswirkt. Außerdem entfällt die Vergaservorwärmung. Der Hubraum beträgt 1352 cm3, die Startleistung 100 PS. Die Zylinderkopfdeckel sind wie beim 100-PS-Vergasermodell grün, die TBO liegt bei 2000 Stunden. Rotax 915 iS: Einspritzanlage, Turbolader und Ladeluftkühlung sorgen für 141 PS Startleistung. Wie bei allen »großen Rotax« liegt der Hubraum bei 1352 cm3. Das Triebwerk bietet elektronisches Motormanagement und optional eine 24-Volt-Lichtmaschine. Die blauen Zylinderkopfdeckel sind markant. Die TBO liegt bei verhältnismäßig niedrigen 1200 Stunden.
Technische Probleme mit Rotax-Motoren
Zeit, die Schutzbrillen abzunehmen und im Meeting- Raum Platz zu nehmen. Es gibt viel zu diskutieren. Mit Innovationen wie neuen leistungsstarken Turbomotoren bauen die Österreicher ihre starke Marktposition aus. Auf der anderen Seite gibt es aktuell technische Probleme: Leistungsverluste vor allem im Startlauf riefen Verbände und Behörden auf den Plan. BRP-Rotax selbst veröffentlichte ein umfangreiches Service Bulletin (SB-912-079) zur Kontrolle der 912er-Motoren samt Hinweisen zu Installation, Bedienung im Flug, Wartung sowie Kraftstoffversorgung.
fliegermagazin: Es gibt Untersuchungen vom Luftfahrt-Bundesamt und den UL-Verbänden zu Leistungsverlusten bei Rotax-Motoren. Was trägt BRP-Rotax zur Fehleranalyse bei?
Andreas Bangerl: Das Thema ist komplex und beschäftigt uns schon seit 2020. Wir haben Leistungsverluste meist in der Startphase und sehen uns zum Teil mit Kolben- und Klopfschäden konfrontiert. Wir nehmen diese Fälle sehr ernst. Meist lassen sich die Schäden nicht auf eine einzelne Ursache zurückführen. Wir haben in Kooperation mit einem Flugzeughersteller herausgefunden, dass auch der Einbau ein Faktor sein kann. Wir haben bereits vor über drei Jahren einen Service Letter dazu veröffentlicht. Der entspricht inhaltlich in etwa dem aktuellen Service Bulletin. Leider wurden seit damals nicht alle von uns vorgeschlagenen Punkte umgesetzt. Das müssen wir akzeptieren.
Die Flugzeughersteller sind unsere Kunden und haben grundsätzlich das Recht, von den Vorgaben abzuweichen. Schließlich hat das Thema die Verbände und die EASA auf den Plan gerufen. Daraufhin haben wir gemeinsam mit den Herstellern Untersuchungen durchgeführt. Das führte zum aktuellen Service Bulletin und bestätigt in etwa die bereits existierenden Erkenntnisse.
Das Service Bulletin betrifft teils Hersteller, teils die Wartung sowie die Motorbedienung durch die Piloten. Wie soll beispielweise ein Verein damit umgehen, wenn Hersteller Motoren nicht SB-konform installieren, aber das neue Luftfahrzeug noch Garantie hat?
Marc Becker: Der Halter kann erstmal nichts dafür. Angenommen, es passiert ein Startabbruch und Auslöser war der unzureichende Durchmesser der Benzinzuleitungen. Damit ist das Problem nicht motor-, sondern installationsbezogen. Dann würden wir an den Flugzeughersteller verweisen. Für uns hat die Sicherheit oberste Priorität. Gleichzeitig richten wir unsere Maßnahmen gezielt an die Verantwortlichen, die die Ursachen effektiv beheben können. Das ist auch Intention unseres Service Bulletins. Wir sagen den Herstellern: Du musst das ändern. Das entspricht nicht den Betriebsgrenzen beziehungsweise Einbauvorschriften des Einbauhandbuchs.
Inwieweit werden die Hersteller überprüft, zum Beispiel, indem BRP-Rotax die Konstruktionspläne zum Einbau der Motoren in die Zelle vorab checkt?
Marc Becker: Gute Frage. Heute gibt es eine solche Prüfung nicht. Es gibt natürlich ein detailliertes Installations-Manual. Wir bieten darüber hinaus über unsere Vertriebspartner oder auch direkt vom Werk zusätzliche Unterstützung an. Auf Wunsch besuchen wir die Hersteller vor Ort. Das ist ein Learning aus den Problemen.
Leider sind nicht alle Hersteller offen dafür. Viele Hersteller arbeiten aber eng mit uns zusammen und zeigen uns die geplante Installation digital bereits in der Konstruktionsphase. Die weisen die Einhaltung der Limits auch nach. Bei EASA-zertifizierten Flugzeugen muss dies sogar geschehen. Im Bereich UL ist die Sachlage anders. Wir setzen alles daran, hier noch entschlossener und aktiver vorzugehen, sind uns jedoch der enormen Herausforderungen und des damit verbundenen Aufwands bewusst. Wir haben 250 OEMs mit gut 400 Flugzeugmustern.
Betreffen die Probleme eigentlich alle Motortypen?
Andreas Bangerl: Die Vergaserversion mit 100 PS, also 912 ULS und 912 S, sind mit Abstand am häufigsten betroffen, vor allem aus technischen Gründen. Sie sind jedoch auch am weitesten verbreitet. Bei den Einspritzern haben wir bei Problemen durch die Elektronik bessere Diagnosemöglichkeiten. Da sehen wir am Log-File die Betriebszustände.
Marc Becker: Der Einspritzer ist aufgrund der Elektronik auch etwas robuster, denn er kann selbsttätig auf Störungen reagieren.
Wie geht es jetzt weiter?
Andreas Bangerl: Wir arbeiten eng mit der EASA zusammen, die auch in die Erstellung des Service Bulletins eingebunden war. Wir haben jetzt etwas am Baum geschüttelt und warten die Reaktionen und Untersuchungen ab. Wir arbeiten auch eng mit OEMs zusammen, die sich bei uns melden. Klares Ziel ist die Verbesserung. Dazu wird es im Bereich der EASA sicher in Zukunft noch weitere Service Bulletins oder Ähnliches geben. Man muss aber auch die Fallzahlen in der Relation betrachten.
Wir haben rund 82.000 Motoren ausgeliefert. Davon gibt es je nach Zählweise zirka 100 Vorfälle. Nicht alle Ursachen sind herstellerspezifisch, wie beispielsweise bei unzureichender Benzinqualität.
In welchem Muster wurden die meisten Rotax-Motoren verbaut?
Marc Becker: Das ist nicht so einfach zu beantworten. Denn wir liefern über unsere Distributoren aus und führen erst seit zwölf Jahren Statistik, wo die Motoren verbaut werden. Absolut gesehen dominieren noch die Zweitakter. Also wird ein Drachenhersteller bester Kunde sein. Bei den Viertaktern gehören Comco Ikarus, Flight Design und AutoGyro zu den großen Abnehmern.
Laufen die Einspritzer den Vergasern den Rang ab?
Marc Becker: Im Jahr 2024 wird der Einspritzer mit 100 PS zum ersten Mal genauso häufig gekauft wie die Vergaserversion. Bei den iS-Motoren verzeichnen wir ein starkes Wachstum. Derzeit verkaufen wir zu etwa zwei Dritteln Sauger- und zu einem Drittel Turbomotoren. Der Trend entwickelt sich aber Richtung Aufladung.
Gibt es die Möglichkeit, nach Ablauf der TBO den Motor im Werk überholen zu lassen?
Andreas Bangerl: Nein, dafür haben wir ein Netzwerk aus Partnern. Es macht keinen Sinn, zum Beispiel einen Motor aus den USA hierher zu schicken. Durch konstantes Training und eine sehr selektive Auswahl der Partner stellen wir einen Service sicher, der der Qualität im Werk in nichts nachsteht.
Was sind global gesehen die wichtigsten Märkte?
Marc Becker: Zentral- und Osteuropa sind die größten Märkte, weil hier die meisten Hersteller sitzen. Den größten Nutzermarkt haben wir dagegen in Nordamerika. Dort sind die LSA-Klasse und Flugschulen wichtige Abnehmer.
Wird BRP-Rotax in die Leistungsklasse über 160 PS Leistung einsteigen?
Marc Becker: Wir beobachten den Markt und Entwicklungen wie MOSAIC in den USA. Jetzt sind dort erst einmal die Proposals veröffentlicht worden. Eine finale Entscheidung ist bei uns noch nicht gefallen.
Welche Ansätze verfolgt BRP-Rotax beim Thema Emissions- und CO2- Reduktion?
Marc Becker: Der Faktor Zeit ist entscheidend. Die Batterien mit ihren derzeitigen Kapazitäten sind noch zu schwer für die Sportfliegerei. Wir verfolgen mehrere Ansätze. Zunächst versuchen wir, unsere Motoren so sparsam wie möglich zu gestalten. Der zweite Schritt sind regenerativ produzierte E-Fuels beziehungsweise SAF. 2021 haben wir einen Rekord mit regenerativem Kraftstoff in einer C42 mit 80-PS-Motor aufgestellt. Wir bleiben da dran. Auch im Bereich Elektro sind wir aktiv. Aber das sehen wir eher als langfristige Lösung.
Zum Abschluss noch eine Frage zu den Kosten. Warum sind viel produzierte Modelle wie der 80-PS-Vergasermotor verhältnismäßig teuer im Austausch?
Marc Becker: Durch die geringen Stückzahlen und die hohe Haftung in der Luftfahrt steigen die Preise bei Zulieferern kontinuierlich. Wir versuchen, einen Teil der Preissteigerungen durch mehr Effizienz im Werk abzufangen und nicht alles an die Kunden weiterzugeben. Beim 80-PS-Motor nimmt die Anzahl in der Flotte ab. Hersteller verbauen den Motor neu nur noch selten. Wir müssen bei sinkenden Stückzahlen also verhindern, dass die Zulieferer abspringen. Das treibt die Preise. Als Firma möchten wir natürlich gerne ein günstiges Einstiegsmodell anbieten, damit wir mehr Menschen in die Fliegerei bringen.
Dirk M. Oberländer, Jahrgang 1975, verbrachte seine Jugend beim Segelfliegen am Flughafen Braunschweig-Wolfsburg. Später folgte der Abschied vom Schieben und Umstieg zum Ultraleicht-Fliegen. Die zweite große Leidenschaft, das Schreiben, brachte Dirk zu Stadtmagazinen, Tageszeitungen, Kundenmedien und in die wunderbare Welt der Werbung. Immer mit einem Faible für Technik und die Menschen dahinter. So war es nur eine Frage der Zeit, bis der studierte Kultur- und Medienmanager beim fliegermagazin landete. Am Boden ist Dirk bevorzugt mit Laufschuhen und Rad unterwegs – im Urlaub auch gern mal mit Zelt in Richtung Süden.
- Rotax
- Flugzeugmotoren
- Rotax 912